Our Latest Thinking & Industry Contributions
News
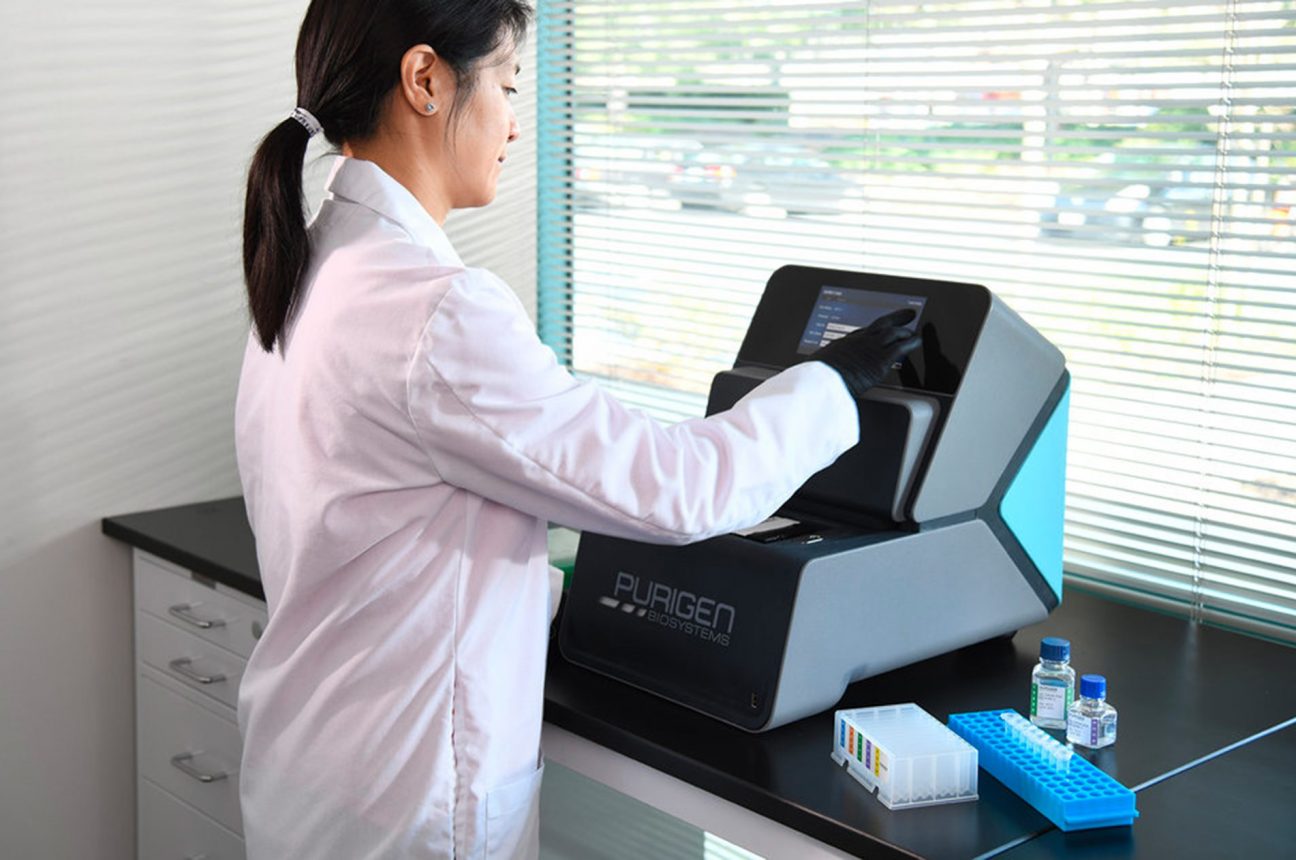
Nuvation Selected for Purigen Biosystems’ Revolutionary DNA Extraction Instrument
Nuvation Engineering provided custom board design, firmware development, and regulatory compliance testing support for Purigen’s revolutionary DNA extraction and purification device. June 12, 2020, Sunnyvale, CA. Purigen Biosystems selected Nuvation Engineering to provide hardware and[…]
Nuvation Engineering - July 3, 2024
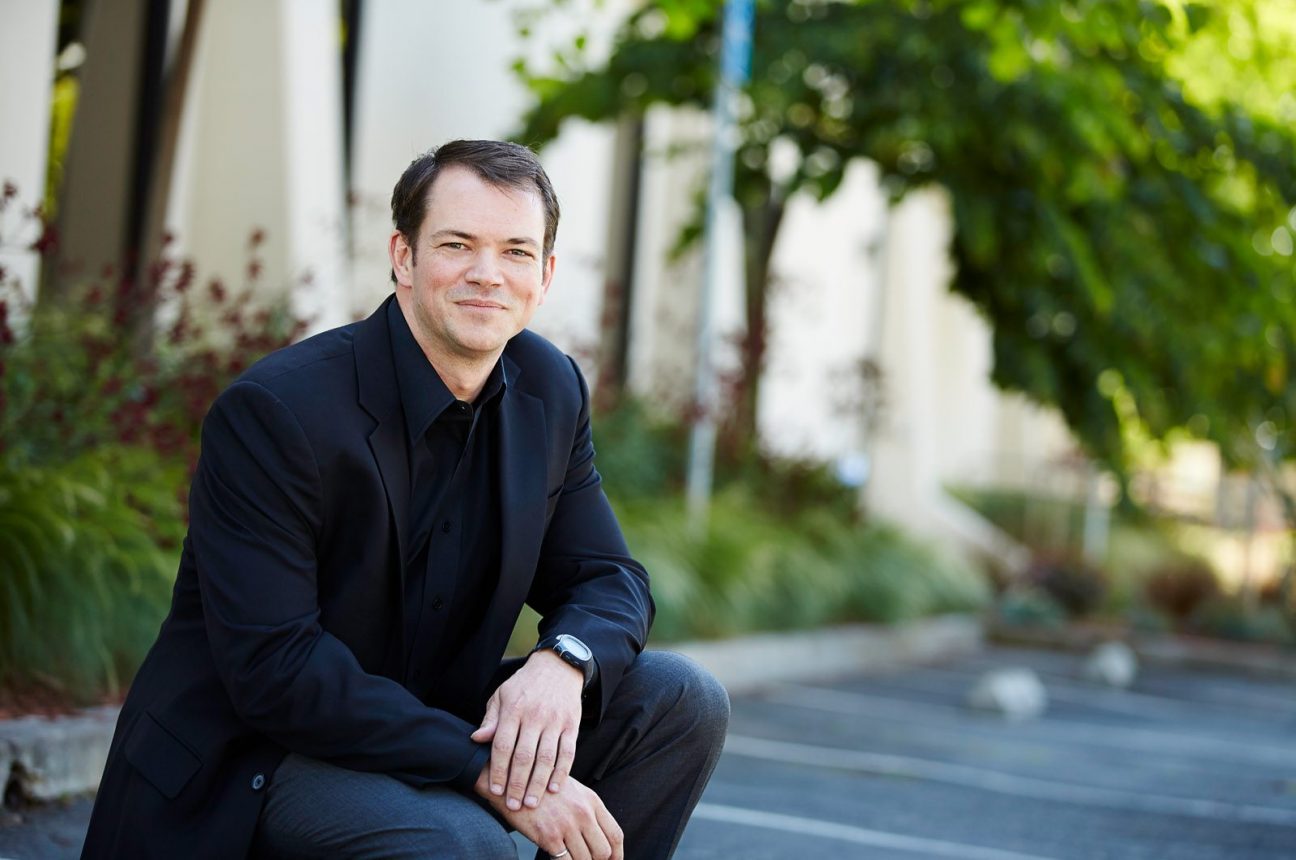
Hardware Bee Interviews Nuvation CEO Michael Worry
Discover the Latest Innovations and Opportunities Shaping the Future of Digital Finance. Stay ahead of the curve with insights into emerging technologies, investment strategies, and market developments in the dynamic world of cryptocurrency.
Nuvation Engineering - April 26, 2024
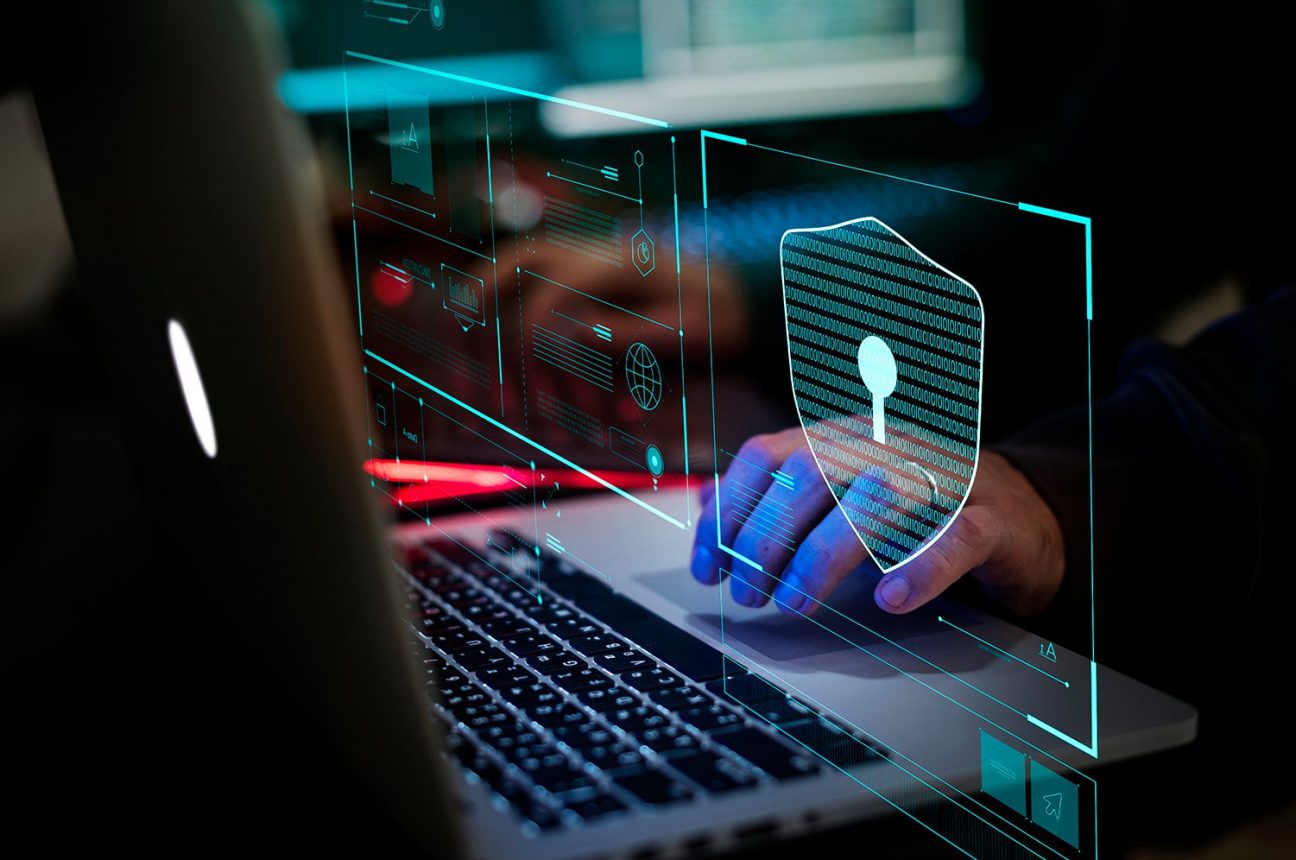
Important Design Considerations for Electronic Devices: Part 4 – Data Security
Over the past two decades Nuvation Engineering has developed electronic devices for a wide range of market applications. Based on our experience across hundreds of engineering design projects, our engineers have identified several[…]
Nuvation Engineering - March 13, 2024
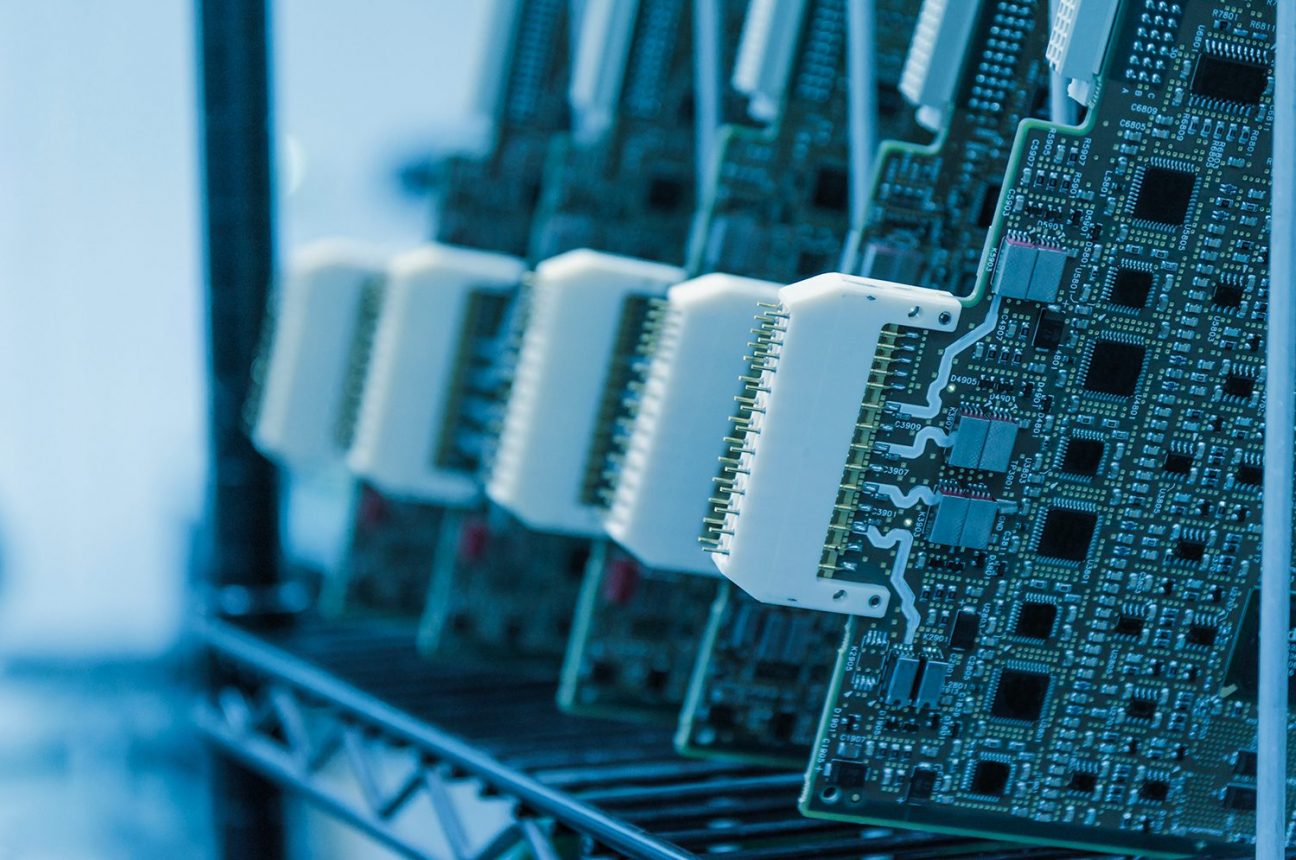
Important Design Considerations for Electronic Devices: Part 3 – Off-the-Shelf Solutions vs. Custom Hardware
Over the past two decades Nuvation Engineering has developed data acquisition systems for a wide range devices and market applications. Based on our experience performing hundreds of engineering design projects, our engineers have[…]
Nuvation Engineering - January 24, 2024
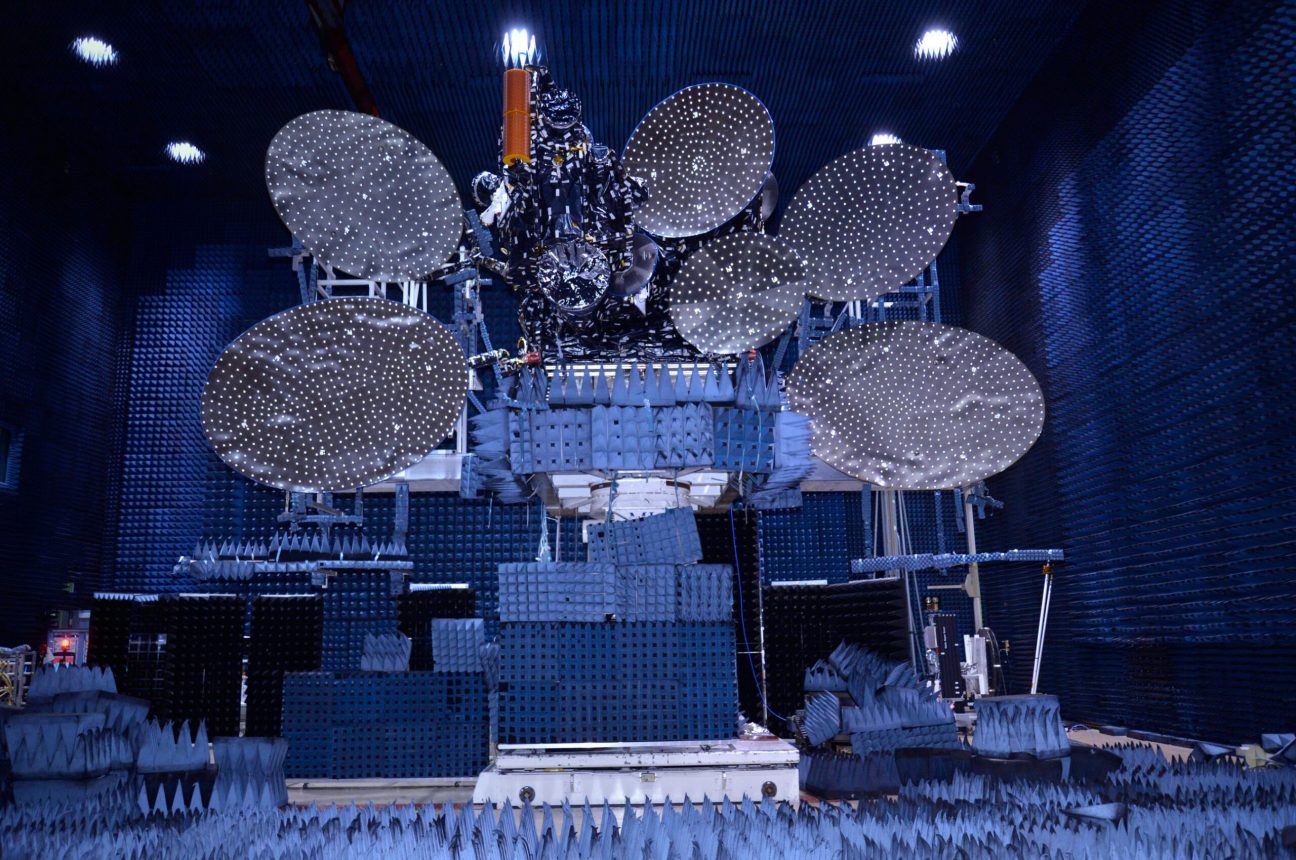
Important Electronic Design Considerations for Electronic Devices: Part 2 – Harsh Environments
Over the past two decades Nuvation Engineering has developed data acquisition systems for a wide range devices and market applications. Based on our experience performing hundreds of engineering design projects, our engineers have[…]
Nuvation Engineering - November 15, 2023
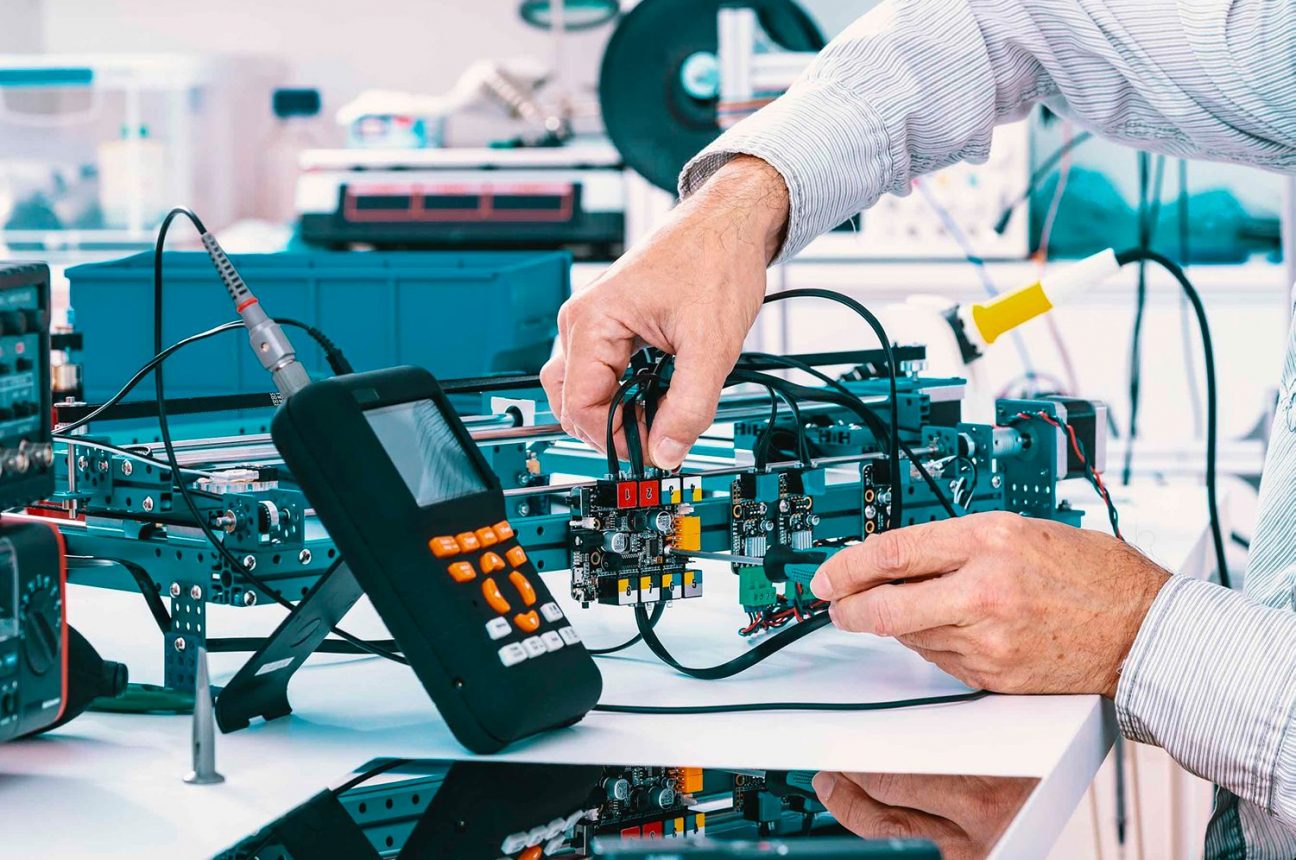
Important Electronic Design Considerations for Electronic Devices: Part 1 – Calibration
Over the past two decades Nuvation Engineering has developed data acquisition systems for a wide range devices and market applications. Based on our experience performing hundreds of engineering design projects, our engineers have[…]
Nuvation Engineering - September 20, 2023
Recent Posts
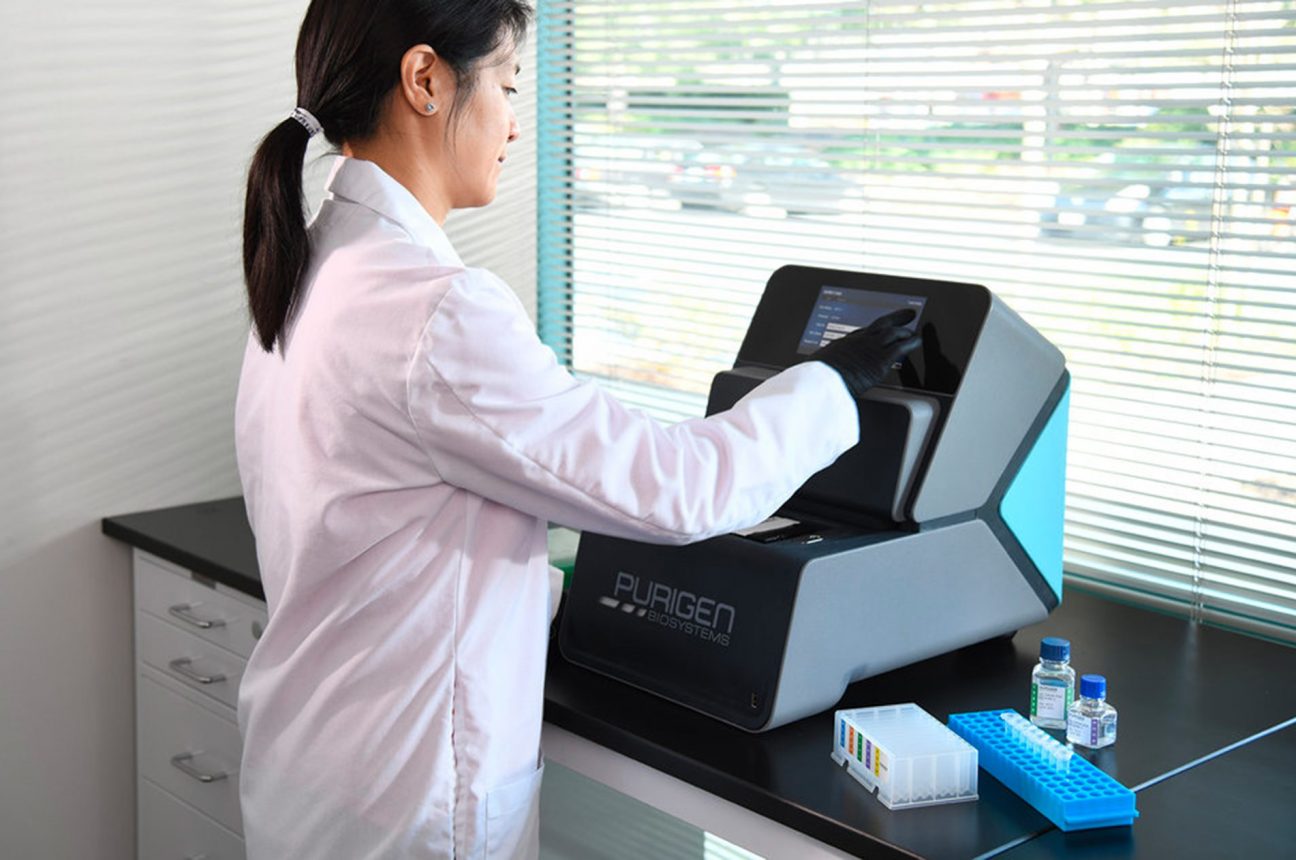
Nuvation Selected for Purigen Biosystems’ Revolutionary DNA Extraction Instrument
Nuvation Engineering provided custom board design, firmware development, and regulatory compliance testing support for Purigen’s revolutionary[…]
Nuvation Engineering - July 3, 2024
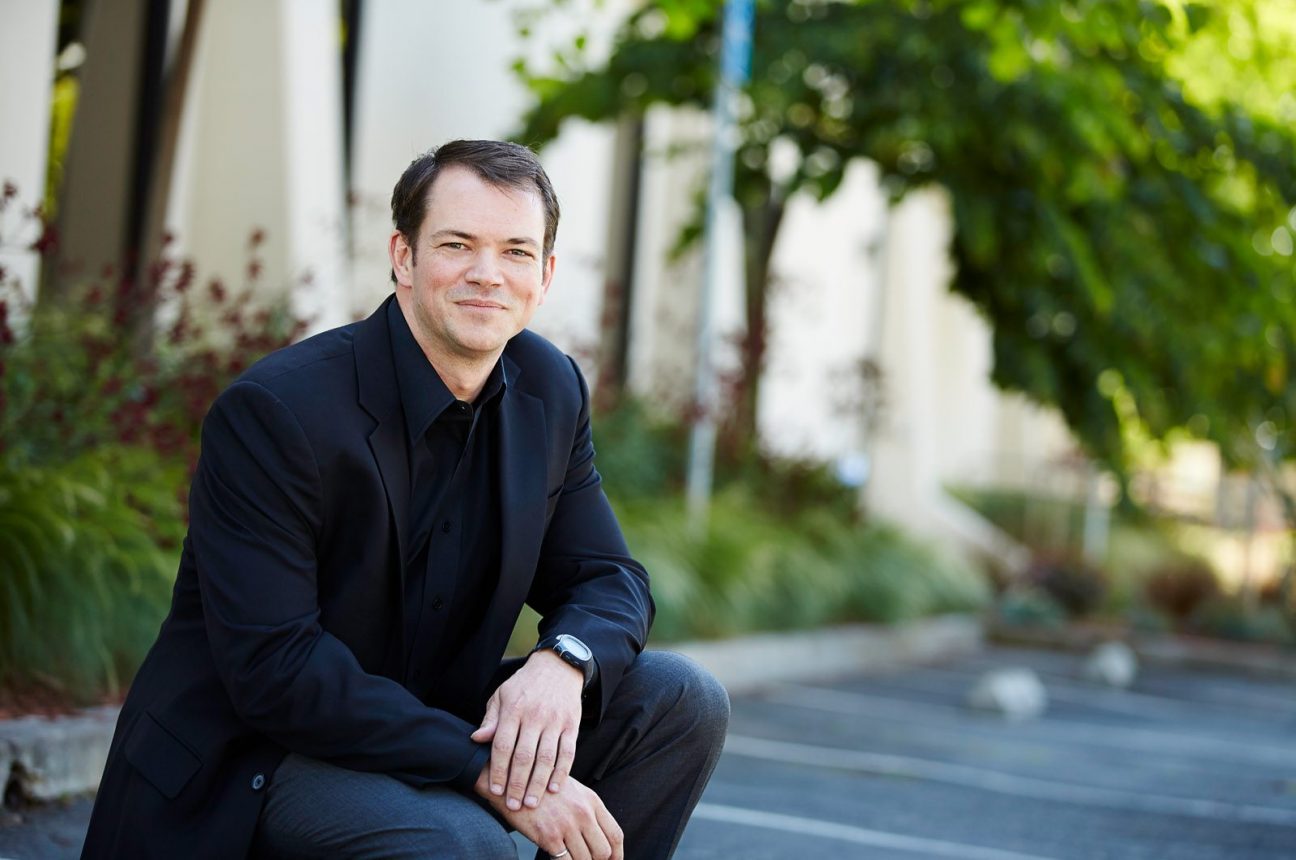
Hardware Bee Interviews Nuvation CEO Michael Worry
Discover the Latest Innovations and Opportunities Shaping the Future of Digital Finance. Stay ahead of the[…]
Nuvation Engineering - April 26, 2024
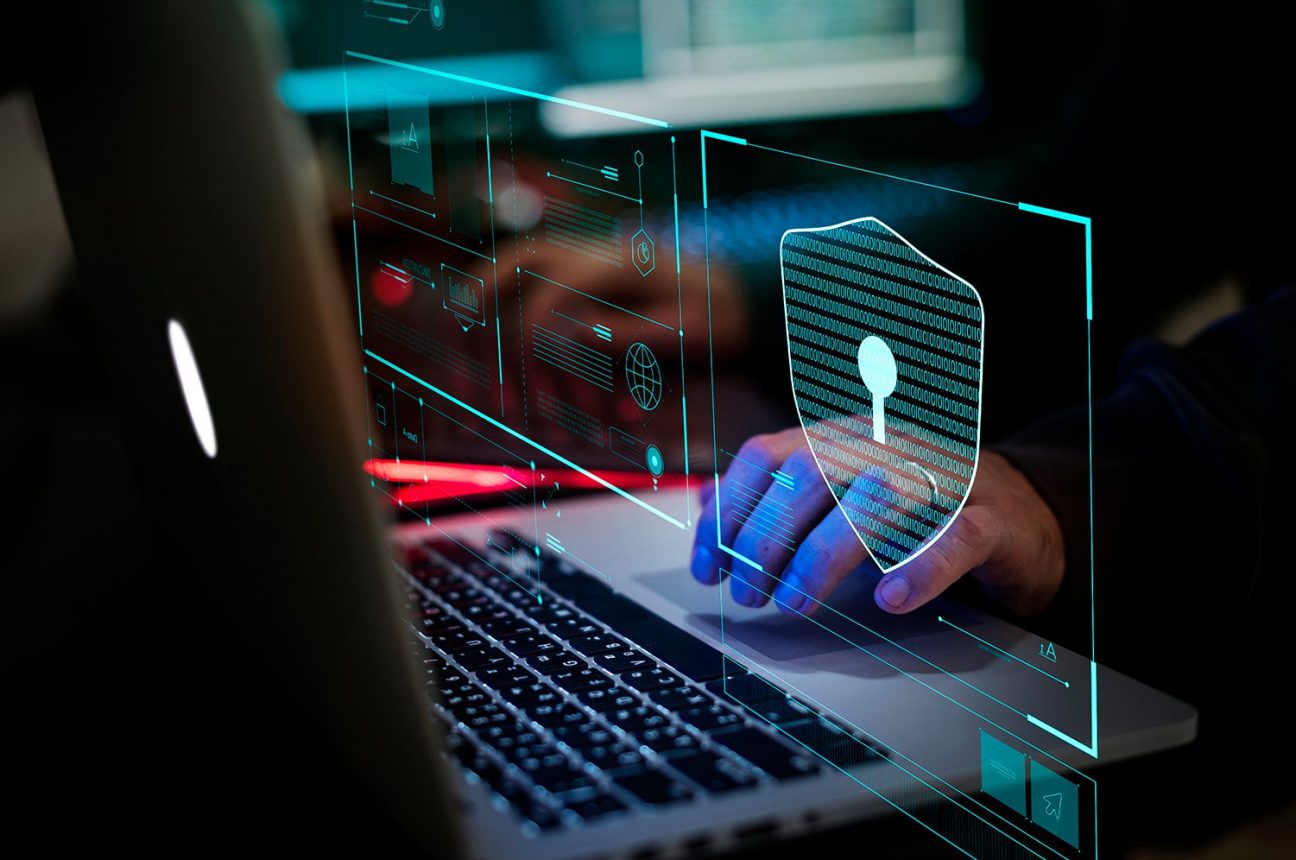
Important Design Considerations for Electronic Devices: Part 4 – Data Security
Over the past two decades Nuvation Engineering has developed electronic devices for a wide range of[…]
Nuvation Engineering - March 13, 2024
Popular Posts
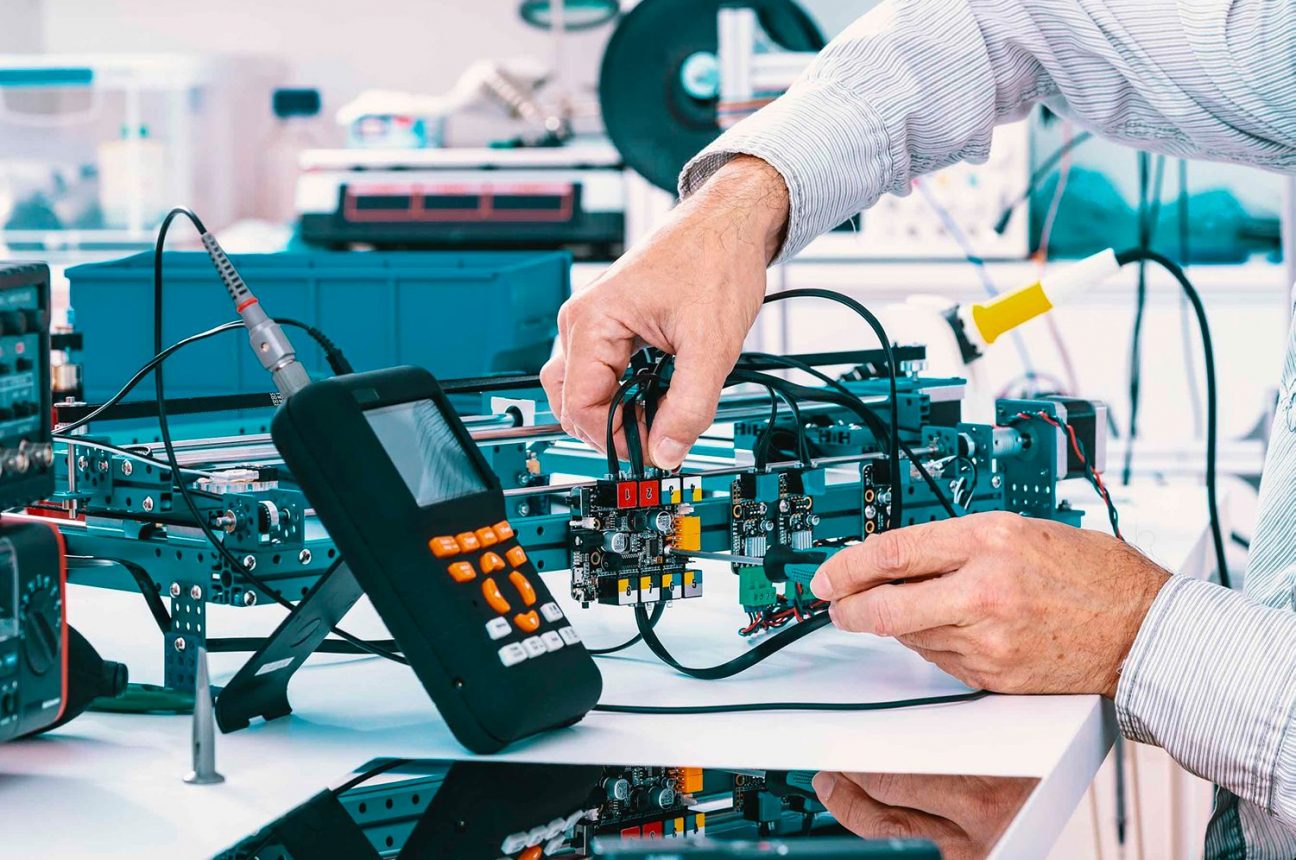
Important Electronic Design Considerations for Electronic Devices: Part 1 – Calibration
Over the past two decades Nuvation Engineering has developed data acquisition systems for a wide range[…]
Nuvation Engineering - September 20, 2023
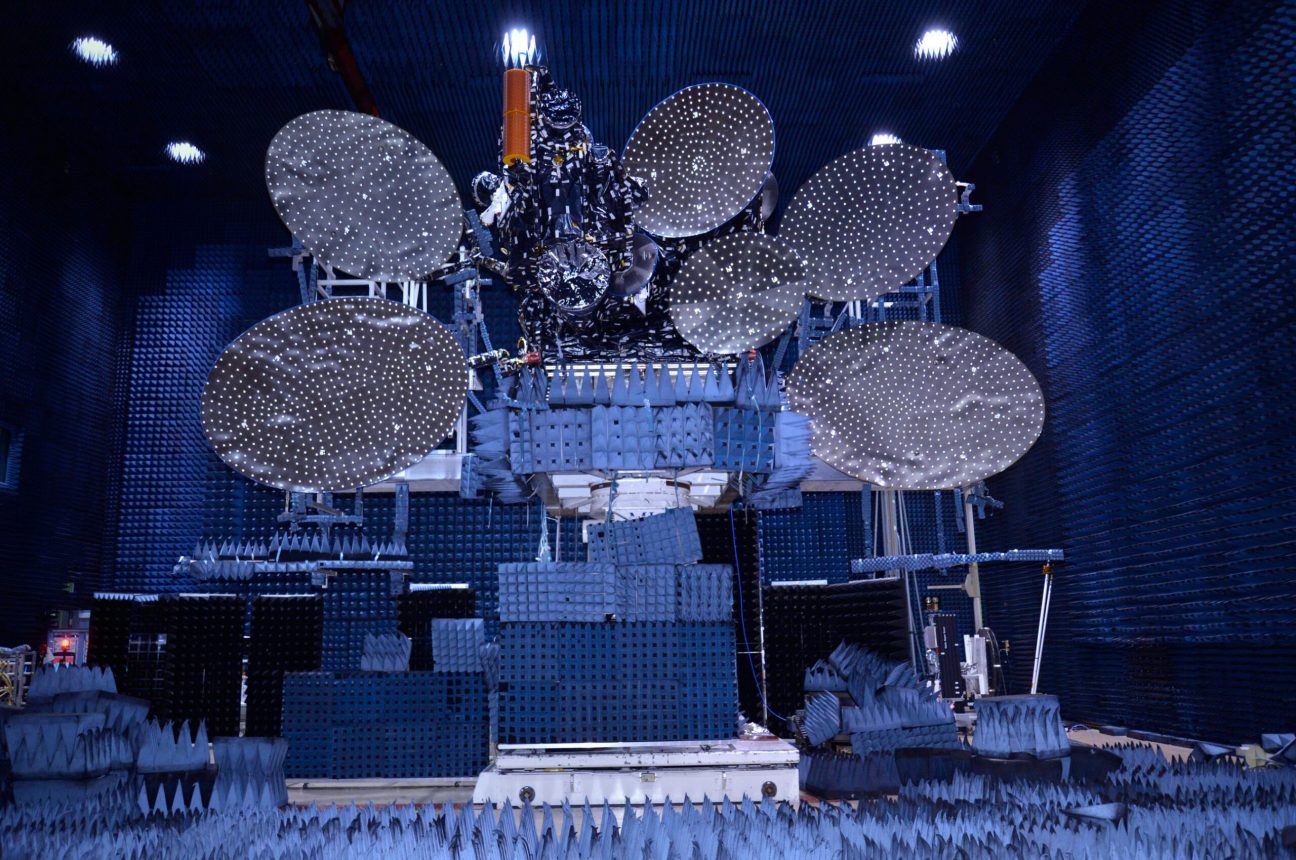
Important Electronic Design Considerations for Electronic Devices: Part 2 – Harsh Environments
Over the past two decades Nuvation Engineering has developed data acquisition systems for a wide range[…]
Nuvation Engineering - November 15, 2023
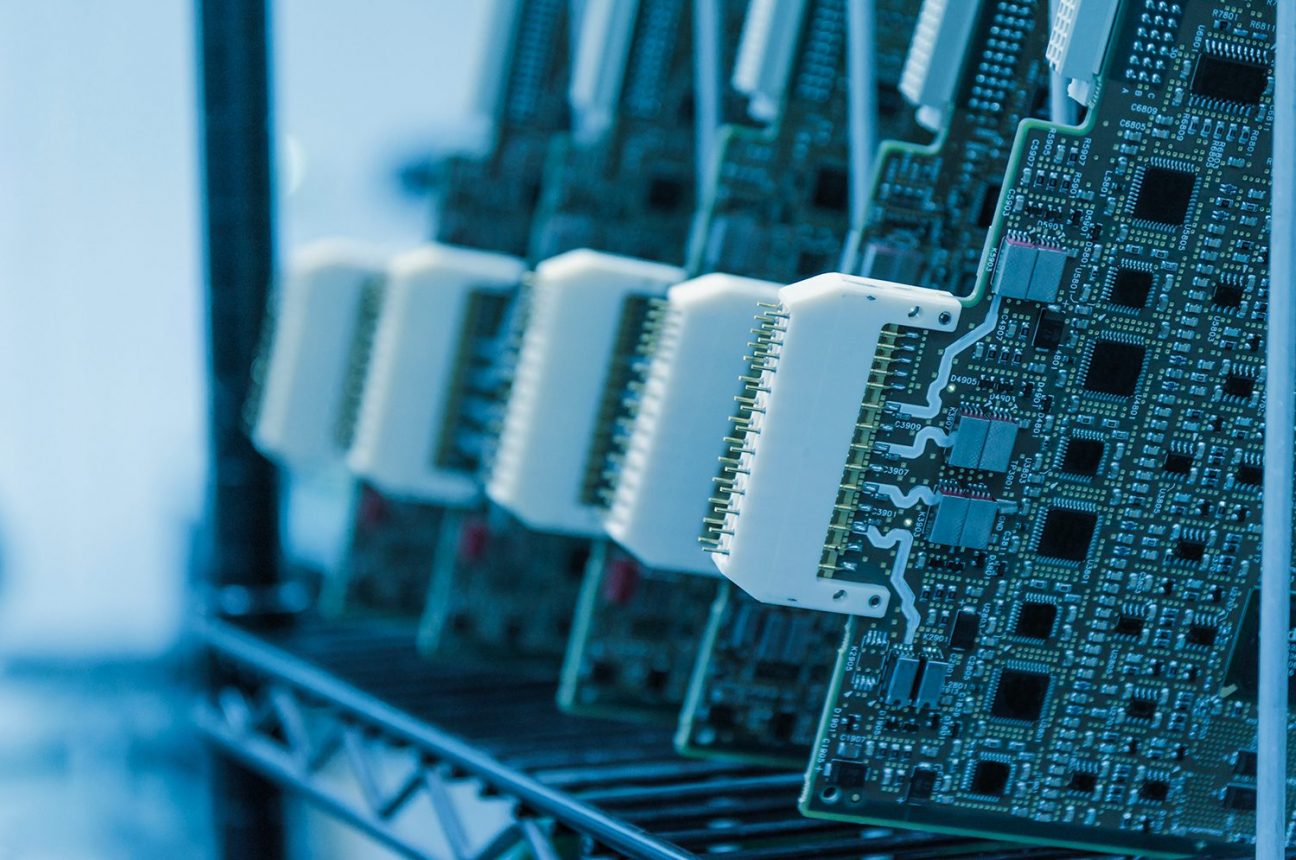
Important Design Considerations for Electronic Devices: Part 3 – Off-the-Shelf Solutions vs. Custom Hardware
Over the past two decades Nuvation Engineering has developed data acquisition systems for a wide range[…]
Nuvation Engineering - January 24, 2024
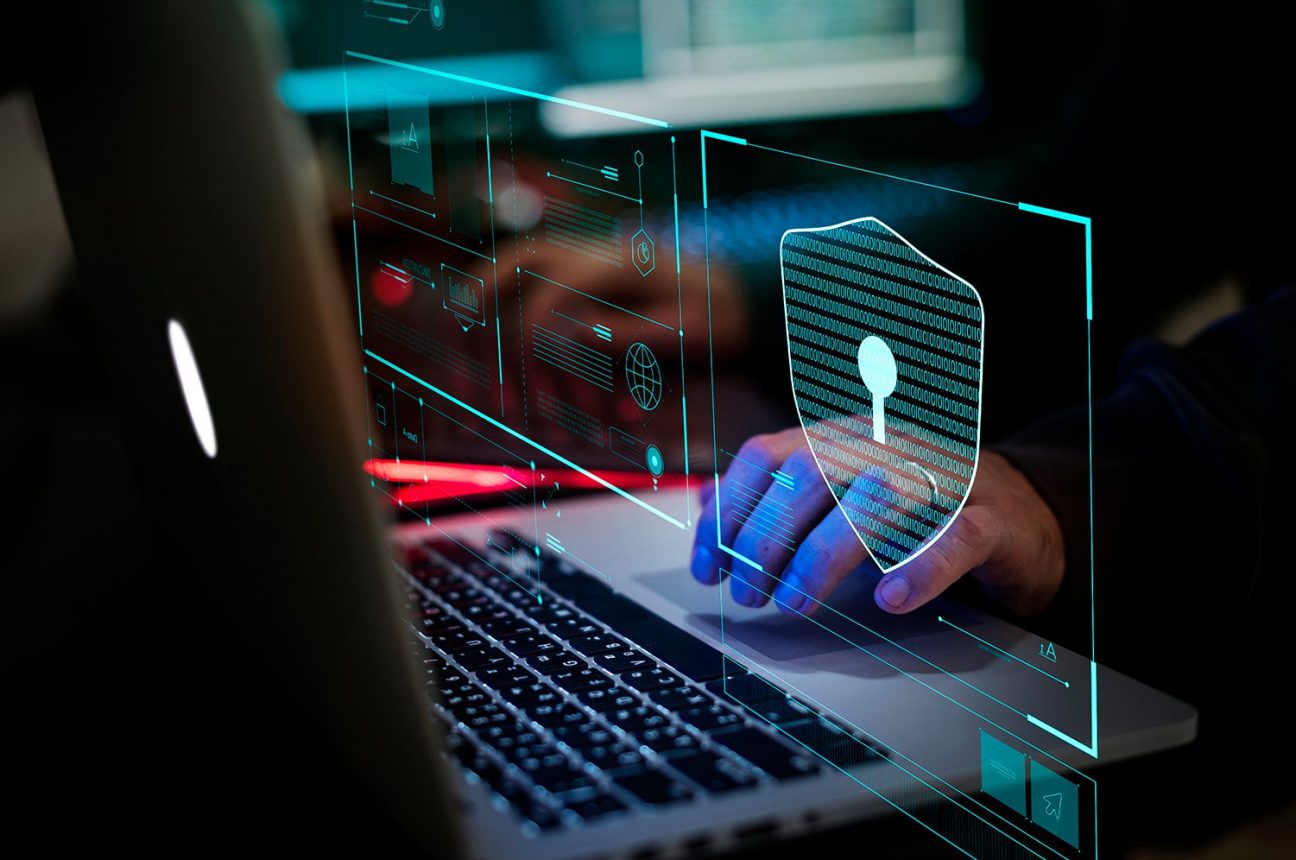
Important Design Considerations for Electronic Devices: Part 4 – Data Security
Over the past two decades Nuvation Engineering has developed electronic devices for a wide range of[…]
Nuvation Engineering - March 13, 2024
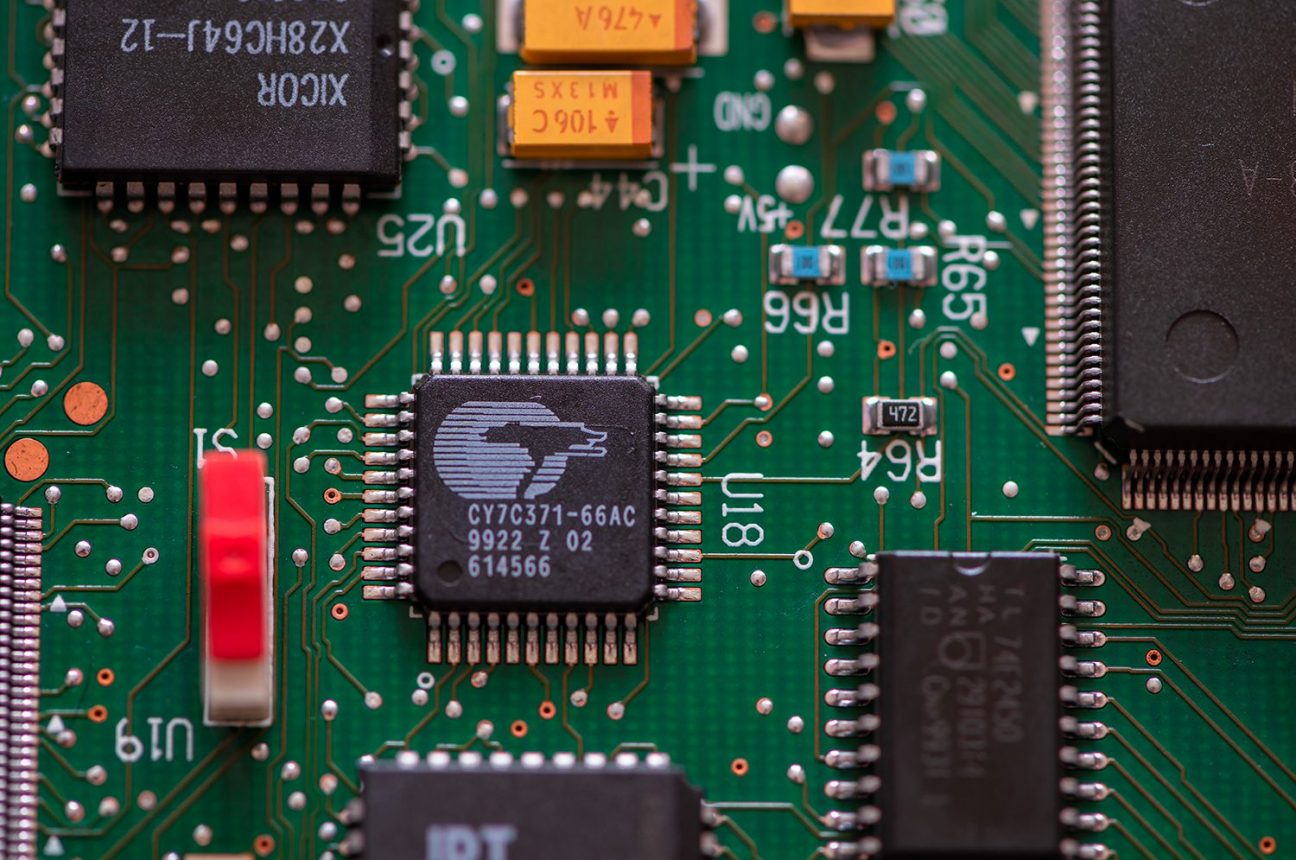
CPLD Trends
Each product originates from a combination of many materials and labor. During manufacturing, direct materials often[…]
Nuvation Engineering - April 13, 2022
Recent Posts
Newsletter
Subscribe to receive the latest news & updates.