Prototyping includes initial product testing, design optimization, and problem identification and resolution prior to volume production. Rapid prototyping can significantly shorten a new product’s time-to-market, but certain trade-off decisions must be made and production challenges anticipated.
Rapid Prototyping Trade-Offs
Cost vs. Schedule
One trade-off to consider when engaged in rapid prototyping is cost vs. schedule. Companies need to decide how much they are willing to pay to shorten the fab and assembly schedules. Prototype PCB fabrication times are typically five to ten days depending on the PCB stack-up and fabrication process. Fabrication can sometimes be accelerated to three days or less, but that tends to come at a significant cost increase. PCB assembly time is typically five to ten days, depending on the number and types of components. Assembly time can be accelerated to three days or less, at yet another cost increase.
Quality vs. Schedule
Quality issues that arise during rapid prototyping can incur additional material costs and extend the project schedule. If fabrication and assembly schedules are accelerated beyond the capabilities of the vendors, it creates the risk of fab or assembly errors. Depending on the severity of those errors, schedules can become pushed out due to additional time spent investigating and repairing boards. In a worst-case scenario, boards can be unusable and require a re-spin.
When engaged in rapid prototyping therefore, one must ask “how fast is too fast?” That question can be answered through frank and transparent communications between the engineering design team and their fabrication and assembly partners. This enables the engineering design team to define quality risks up front and make well-informed trade-off decisions in consultation with the client.
Complexity vs. Schedule
Another key decision when performing rapid prototyping is to weigh complexity vs. schedule. This involves evaluating the importance of product design risks vs. time-to-market pressures. For example, a complexity vs. schedule trade-off may involve deciding what form factor, PCB stack-up, and fabrication process to use. For example, a fully micronized prototype that requires a High-Density Interconnect (HDI) stack-up or a rigid-flex board will incur additional layout time and can take up to four weeks for fabrication. An alternative approach that could reduce fabrication time to one week or less would be to develop the prototype in a larger form factor and to use a standard thru-hole via stack-up. This would allow design teams to get prototype boards sooner and begin assessing critical circuit functionality and performing software integration and testing.
Rapid Prototyping Challenges
Communication and Coordination
Fabrication and Assembly Issues
In order to minimize fabrication and assembly issues, the product should be designed to meet the vendor’s DFM and DFT guidelines.
DFM is achieved by sharing board requirements with fabrication and assembly vendors during the early stages of product development, and coordinating with them around stack-up decisions, component packages, and fabrication and assembly processes. This helps to ensure first-time-right production.
DFT should begin during the product’s design phase in order to determine the best way to test the board after assembly. An example of this would be to include adding test points on a selection of nets that will be used in a manufacture test rig; the test rig verifies the assembly for shorts, corrects resistors, and ensures all components have been installed correctly.
Planning, Communication, and Project Management
The vast majority of the effort of de-risking rapid prototyping efforts resides in detailed up-front analysis of design complexity vs. schedules, and effective communication with fabrication and assembly vendors. This ensures that all project participants are making well-informed decisions.
When the final deliverable is a micronized design, the initial development of larger and simpler prototypes can accelerate project completion by enabling software integration and testing to begin in parallel with the development of the micronized product.
The key to success is to work with a design team that possesses the experience needed to navigate all of these requirements, and has trusted fabrication and assembly partners with whom they have built strong relationships over many projects. With over 20 years of experience in electronic design projects and 1000+ projects completed, we encourage you to consider Nuvation Engineering for your next rapid prototyping and product development project. Contact us for a quote.
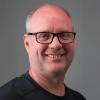