By Neil Miller | Nov 27, 2013
In our previous post we discussed why design validation testing (DVT) is so important for electronic product designs, and described how electronic and electromagnetic tests were performed. Next we’ll take a look at environmental DVT and how it can ensure the reliability of an electronic product in all conditions.
The objective of environmental DVT is to verify that a prototype design satisfies product requirements for various environmental operating conditions such as temperature, humidity, altitude, water and dust exposures. Consumer electronics are not usually expected to withstand extreme conditions, but products for applications such as military or aerospace will have a much wider operating range.
Temperature
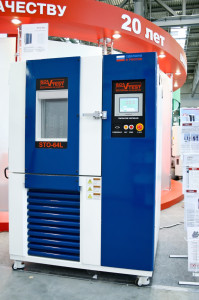
Temperature testing (or Thermal Cycling) validates product operation within specified operational temperature limits. Humidity testing can be phased in with the operational temperature tests so that all conditions can be represented. The duration of thermal testing will vary depending on the application, and can range from a few hours to many days. The figure below shows a thermal cycle profile for a product used in an industrial environment. In this case the product was tested between 0°C to 50°C 70±5% RH for duration of approximately 3 days.
Temperature tests can also include scenarios where the product is not expected to be operational, such as storage environments, or situations where the product has been exposed to cold and hot temperature conditions for an extended period of time (e.g., left in a car during hot and humid or sub-zero conditions). For these test conditions a product undergoes a cold and a hot temperature soak for an extended period of time, and is then powered up to verify correct operation.
Pressure
When a product is used in at higher altitudes or in an air transportation environment, altitude testing (also known as or reduced pressure testing) is required to validate operation under varying pressure conditions. Air pressure above sea level is calculated as follows:
p = 101325 (1 – 2.25577 10-5 h)5.25588
where:
- p = air pressure (Pa) and h = altitude above sea level (m)
The altitude for a typical transatlantic flight is 35,000 to 39,000 feet above sea level. Inside the cabin, the pressurized altitude is equivalent to 5,400 to 7,000 feet above sea level. The level and the duration for pressure test will depend on the end application of the product being tested. Common pressure testing standards include RTCA DO-160 Section 4 and MIL-STD-810 500.5.
Water and Dust Ingression
Products that are used in an outdoor environment will be susceptible to exposed to rain while in operation, and products geared towards industrial environments are likely to be exposed to dusty conditions. Design validation should include tests for these environmental conditions to ensure the product provides the acceptable level of water and dust ingress protection.
Products are usually tested to meet a classification within the Ingress Protection (IP) rating system, as shown in the table below. The IP system categorizes products according to the degrees of protection from solid objects and liquids such as water and dust.
IP Number | Solid Objects | Liquids |
0 | No protection | No protection |
1 | Protection against accidental touch by hands | Protection against vertically dropping condensation |
2 | Protection against objects such as fingers | Protection against direct sprays of water up to 15 degrees from vertical |
3 | Protection against tools and wires | Protection against direct sprays of water up to 60 degrees from vertical |
4 | Protection against tools, wires, small wires | Protection from sprays of water in all directions. Limited water ingress permitted |
5 | Limited protection against dust | Protection from low pressure jets of water in all directions. Limited water ingress permitted |
6 | Protected from dust | Nearly the same as # 5, except for ship decks |
7 | Not applicable | Protected against the effects of immersion in water to depth between 15 cm and 1 meter |
The IP classification is a two-part numbering system (for example, IP67). The first number ranges from 0 to 6 and indicates a progressive level of protection against solid objects. A value of 0 indicates no special protection against solid objects and a value of 6 means protection against ingress of fine particles (i.e. dust) is provided. The second number ranges from 0 to 7 and indicates the level of protection for liquids; 0 meaning no protection and 7 some a level of protection for water immersion.
In the next post we take a look at mechanical DVT and the various methods of ensuring the mechanical integrity of an electronic product.
Nuvation Engineering can provide design validation testing support through our New Product Introduction service. As part of this service we prepare test plans and test procedures tailored to customer requirements. We can also develop supporting test software to monitoring the behavior of the product under test during DVT. We work with local test houses to determine an overall DVT program tailored specifically for the products end application. Contact us to discuss your testing and electronic design services needs.