By Aaron Schellenberg | Jan 2, 2014
At Nuvation Engineering, we’re known for our impressive track record of first-time-right designs and our ability to dramatically accelerate development schedules. Just recently we completed a High-density Interconnect (HDI) PCB design based on a Xilinx Virtex-7 FPGA with numerous 933MHz DDR3 memory buses, multiple PCI Express Gen 3 endpoints, and FDR Infiniband (56Gbit) off-board links, all on a (slightly modified) PCI Express card form factor. We delivered the board to the client on budget, 100% functional, and with no ‘blue wires’.
When it comes to HDI PCBs, particularly those with complex FPGA designs, every board is different. If you have a fixed PCB form factor (size, shape, and especially board thickness) there are many things you need to consider. Here are some techniques we use to avoid potential design iterations and costly PCB respins.
4 Helpful Techniques
1) Start with a space study
During the PCB space study, the engineer maps out how the critical components will fit into the available board area. Critical components include FPGAs or processors, power supplies, ICs, and anything with significant size or height. This is done early on in the design phase so that risks can be identified as soon as possible. Potential problems could lead to component substitutions, PCB form factor modifications, or even fundamental changes to the hardware architecture. The space study is not a final component placement, of course; it’s a tool to help identify potential layout issues before the design gets too far underway. Clearly, it is best to make any necessary design changes sooner rather than later.
A thorough space study should be adequate for a seasoned board designer to make a judgment call regarding the technical requirements of the PCB. Outputs from the space study may include:
- An approximate placement of the major components and routing channels
- The estimated layer count requirements for power and signal routing
- A preliminary PCB stackup
- The general layer assignments for the various buses and signal classes
- The estimated trace lengths and worst-case layer transitions for any critical high-speed signals
- A board-level power distribution and grounding strategy
- An estimate as to whether any advanced PCB fabrication technologies may be required, such as microvias, blind/buried vias, narrow traces, etc.
- An approximate representation of where the component power dissipation occurs on the PCB
The space study is not just a simple mechanical drawing based on component package sizes; it is a preliminary layout exercise done in CAD software (such as Altium Designer, Cadence Allegro, or Mentor Expedition), in which all design aspects of the board are considered simultaneously. The emphasis here is that it must be done early in the design phase – often before schematic capture has started – in order to limit design iteration cycles.
2) Perform pre-layout signal integrity analysis
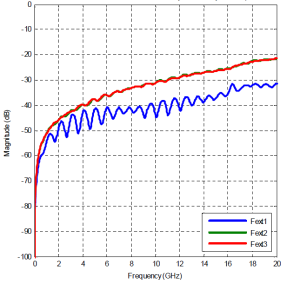
The results of the space study will provide crucial input for getting started on pre-layout Signal Integrity (SI) analysis. One does not need to wait until the board routing is complete in order to perform SI analysis. With a preliminary stackup, layer assignments, and estimated trace lengths in hand, it is a good time to run pre-layout simulations using a 3D field solver to validate the selected components and the topologies of the high-speed signals. This is particularly important for routing to an FPGA with tight trace length or length matching requirements. Layout constraints can then be generated for routing the board based on the SI simulation results. This will help avoid numerous design iterations, as the post-layout SI simulations on the physical design should then only lead to minor design tweaks and refinements. By doing the space study early on in the development, the pre-layout SI analysis can take place in parallel with the detailed schematic work, which allows us to minimize the development schedule.
3. Think about layer count
Often one of the most constraining design requirements in an HDI board is the overall PCB thickness.
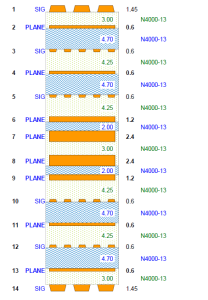
For example, consider the situation where we are designing a PCI Express Add-in card that needs to fit into a 1.57mm edge connector. This limits the layer count to at most 16 layers in many situations – and often less, depending on signal impedance requirements. Furthermore, HDI PCB designs tend to feature power-guzzling FPGAs and processors that require 1oz and 2oz copper planes to distribute the power around the board.
These heavier copper weights will increase your plane thickness and make it even harder to stay within your desired board size. By considering your layer usage up front in your space study and assigning groups of signals to the layers in your stackup early on, you can help prevent a situation later in the design cycle where you are going to increasingly more exotic PCB fabrication techniques just to get your design to fit.
4. Consider thermal management
The space study, along with power dissipation estimates for the major components on your board, can provide the necessary input to perform a preliminary thermal analysis of your design using thermal modeling software. A mechanical engineer can work in parallel with the hardware engineer to ensure that there is adequate airflow across all areas of the board, with no blockage from components or board features. Appropriate heat sink sizing, forced airflow rates, and local component-level fan requirements can be determined early on so that an allowance can be made for these in the design, and you avoid the risk of your FPGA or main processors overheating. It is important to have a good idea as to how the board will behave thermally in its intended environment prior to starting the detailed layout.
In the field of electronic design there is no substitute for experience. Veteran design engineers will be able to assess the complexity of the design early on in the development phase and have an intuitive feel for how cleanly the board will route. As a junior engineer you can get a jumpstart on the learning process by familiarizing yourself with Design for Manufacturability guidelines and consulting an expert wherever you can.
Nuvation Engineering’s experienced engineering teams have delivered over 800 electronic design services projects for a wide range of industries and applications. Contact Nuvation Engineering to learn how we can improve the time to market for your products.